Manufacturing Facilities - Kirloskar Pneumatic
Helping manufacture customer-centric solutions.
Our state-of-the-art manufacturing facilities are flexible and consistently delivers orders promptly and reliably. We have consistently modernised by regularly investing in manufacturing processes. Our investments in our facilities are geared towards reducing delivery time, improving processes and delivering quality and consistency.
Our manufacturing set-up is tooled for in-house machining of critical parts like Crankcase, Connecting rod and dynamic balancing of Crankshaft and Motor pulleys etc. Flexible & optimized manufacturing set-ups are proven for quick set-up changes to prioritize any model based on customer requirement, in product range of 1 cylinder to 12 cylinder compressors. Our pre-treatment shop covers 100% stress relieving & phosphating of each Crankcase while our machine shop is equipped with the latest CNC machines like HMC & VMC, Balancing machines, VTL and in-line quality gates to generate records. Our assembly line is equipped with torque tools to deliver a precise range of torques and quality gates at various locations generate real time quality data.
KPCL has developed manufacturing infrastructure to accommodate manufacturing of 1 CNG Compressor per day. On an average we are looking at an output of 300 Compressors annually. Our manufacturing shed has two bays with crane capacity of 50 tons – 2 Nos and 20 tons – 2 Nos. We have an unique CNG testing bed facility where we can test CNG packages from 200 to 3600 SCMH capacity with suction pressure of 3 kg/cm2G to 40 kg/cm2G and discharge pressure upto 255 kg/cm2G. We have CNG storage capacity of 7000 water liters (2000 ltrs -2 Nos & 3000 ltrs – 1 Nos) where we can test four motor driven packages/two engine driven packages at a time. This test bed facility is a closed loop system consisting of multistage Pressure reduction scheme which reduces pressure from 255 kg/cm2 G to desired suction pressure and piping is looped with heat tracing to maintain desired suction temperature as per client requirement. Our CNG motor driven and engine driven compressor packages are tested in full load condition and all the parameters are recorded. Various alarm and trip condition are also being tested to ensure the working of safety interlocks. KPCL’s Gas Compression facilities are also part of this large set up and a prime requirement which we have added to this has been in house Radiography Room / Shot Blasting and Specialized Painting Room. This ensures that products can be tested and manufactured upto world class standards. In addition to this we are now planning to offer packages to client, so that they can inspect the packages from remote by just sitting in their office during this Covid-19 period.
In-House Technology and Infrastructure
KPCL has one of the most modern screw cutting plant in the world today . We manufacture state of the art air ends designed with the help of SRM and City University – undisputed pioneers and leaders in screw profile design . Highly sophisticated fully automatic screw milling and grinding machines produce screw rotors in temperature controlled conditions to extremely close tolerances .These rotors are checked with the latest rotor profile CMM machines to ensure our screw compressors exceed our customer’s quality expectations.
We have one of the most modern machine shop in the country. Our shop is equipped with numerous horizontal and vertical CNC machining centers, SPM , VTL , boring, grinding and general purpose machines to produce the high quality components required in the manufacture of piston , screw and centrifugal air ends. In fact we are the only compressor manufacturer in India machining API 672 centrifugal impellors with dedicated 5 axis milling machines. Our in house capability includes machining high speed gear boxes for these centrifugal compressors
We have our own foundry dedicated to the manufacture of highly intricate castings used for in house consumption . Thus facility along with our NABL approved laboratory and heat treatment facility gives us the flexibility to meet customized requirements specially for oil and gas , nuclear and defense customers.
The highest quality standard product are assembled under supervision of expert team in our lean assembly shop.
Heat Treatment Facility
Why Heat treatment required
KPCL supplies gears & gearboxes for all critical application where wear resistance at surface is critical & core toughness to be retained simultaneously.
It calls for controlled heating & cooling to alter mechanical properties of Steel at desired location to suit application its designed for. Microstructure of steel is modified to achieve fine tempered martensite at CASE (Surface) & Low carbon martensite at CORE. Retained Austenite % can be restricted within 5%.
KPCL scada controlled facility has state of art machinery at helm of skilled task force to achieve required results as per Design specification with minimum rejection & rework.
In-house Shot pinning Facility improves fatigue life & induced compressive strength of Heat treated component.
Capacity -
Furnace type | Tonnage Capacity | No of Furnaces | MAX Dimensions for Charge |
Pit type Electrical Furnace - Gas Carburising Furnace | 1 | 3 | Dia 1000 X 1390 mm |
2 | 1 | Dia 1300 X 1800 mm | |
3 | 1 | Dia 1500 X 1600 mm |
Quench Tank capacity -
- Tank No.1 :- Round tank with Ø1200 mm and depth 2000 mm having volume 20000 Ltrs.
- Tank No.2 :- Rectangular tank with size (L X W X H in mm) 7700 X 1900 X 2500 and capacity 32000 Ltrs
Salient Features -
- Process controlling is by SCADA software. No manual intervention hence precise control on process.
- SCADA system facilitated with alarm system and real trend charts.
- Periodic calibration of furnaces by thermal mapping and nine point study.
- All sensors are calibrated in NABL laboratories.
- Minimum temperature variation across entire volume of furnace.
- Compatibility of processes like Case Carburising, Hardening, Tempering, Stress Relieving, Annealing, Normalising, Volume Hardening etc.
- Quenching Process is insulated from electric power failure through dedicated Diesel Generator.
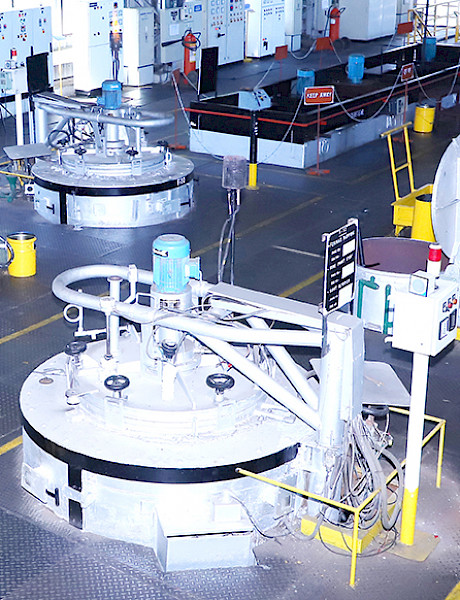